Hydraulic Tube Fittings Manufacturer: A Comprehensive Guide
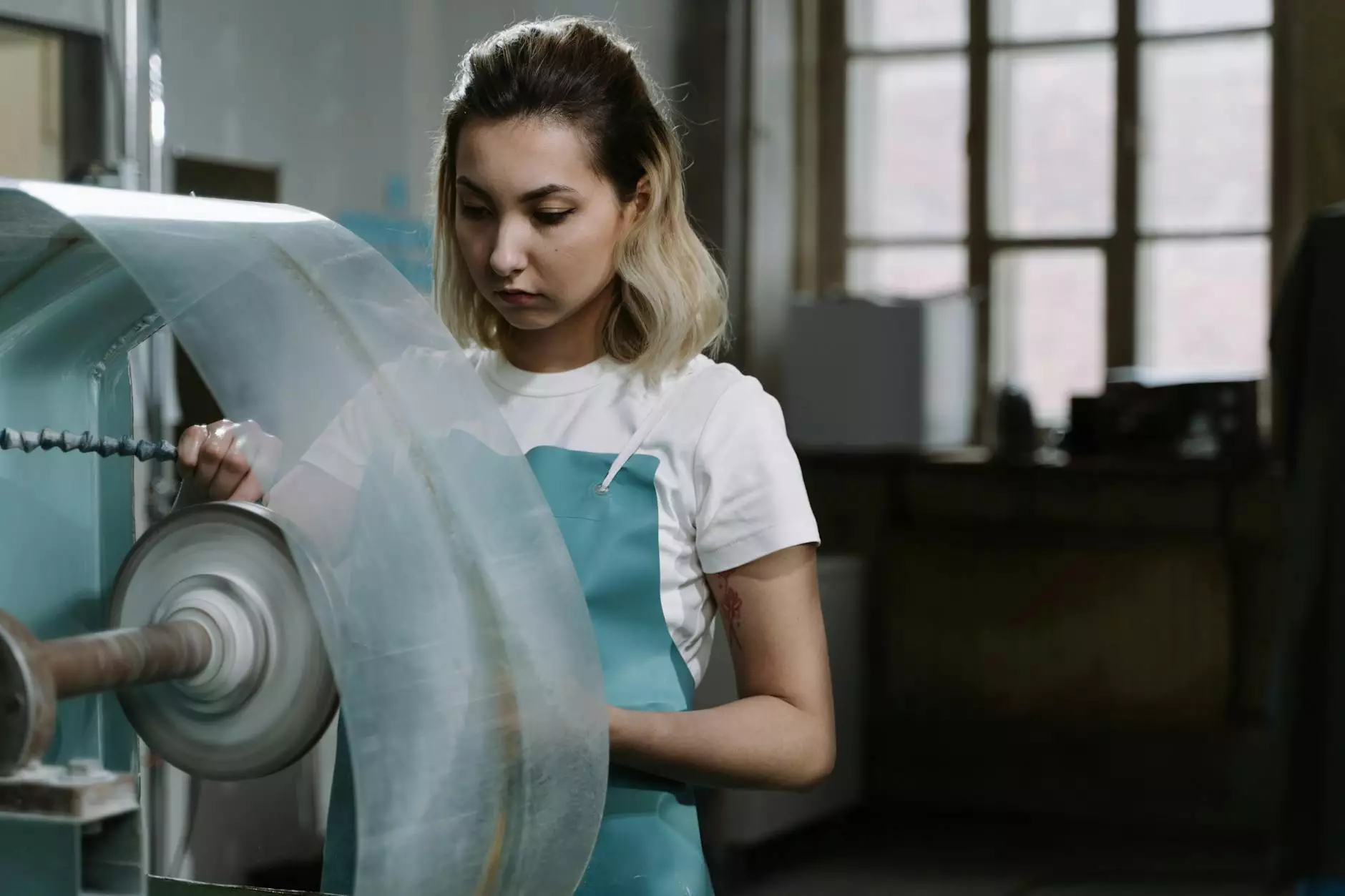
In the ever-evolving landscape of industrial hardware, hydraulic tube fittings play a pivotal role in ensuring reliability and efficiency within hydraulic systems. As a leading hydraulic tube fittings manufacturer, Fitsch (found at fitsch.cn) provides an extensive range of high-quality fittings tailored to meet the demands of various industries. This article delves deep into the world of hydraulic tube fittings, emphasizing their importance, the manufacturing process, and why choosing the right manufacturer is crucial for your business.
Understanding Hydraulic Tube Fittings
Hydraulic tube fittings are components that connect two sections of a hydraulic system, allowing for the efficient transfer of fluids under pressure. These fittings are essential in the maintenance of high performance and safety within machinery, equipment, and pipelines. Available in various sizes, materials, and types, hydraulic tube fittings must be carefully selected based on their application and working environment.
The Importance of Hydraulic Tube Fittings
Hydraulic tube fittings play a critical role in various sectors, including:
- Manufacturing: Essential in machinery that requires high-pressure fluid transfer.
- Automotive: Used in braking systems and power steering systems.
- Aerospace: Vital for hydraulic systems that control flight operations.
- Construction: Employed in heavy machinery like excavators and bulldozers.
As a result, the reliability of these components directly affects the overall performance and safety of the equipment they comprise. Hence, investing in quality fittings from a reputable hydraulic tube fittings manufacturer is of utmost importance.
Types of Hydraulic Tube Fittings
Hydraulic tube fittings come in various types, each designed for specific functions. Here are some commonly utilized fittings:
1. Compression Fittings
Compression fittings are used to join two pieces of pipe together. They provide a tight, leak-proof seal by compressing a ring or collar on the pipe’s surface. These fittings are ideal for applications requiring frequent disassembly.
2. Flared Fittings
These fittings feature a flared end which connects to another flared fitting for a secure connection. They are essential in high-pressure applications where a strong seal is required to prevent leaks.
3. Welded Fittings
Welded fittings are integrated into the piping system during manufacturing, providing a permanent joint. These fittings are ideal for high-stress and high-temperature environments due to their robust nature.
4. Push-to-Connect Fittings
These innovative fittings allow for quick and easy assembly without special tools. They are gaining popularity for their ease of use and effectiveness in low-pressure applications.
The Manufacturing Process of Hydraulic Tube Fittings
The process of manufacturing hydraulic tube fittings is intricate and highly technical. Here’s an overview of the steps involved:
1. Material Selection
The first step in the manufacturing process involves selecting high-quality materials such as stainless steel, brass, or carbon steel. The choice of material is crucial as it affects the fitting's strength, resistance to corrosion, and ability to withstand high-pressure conditions.
2. Machining
Once the material is selected, precision machining is employed to create the fitting’s components. This process may involve turning, milling, or grinding to achieve the required dimensions and tolerances.
3. Heat Treatment
Heat treatment is often necessary to enhance the mechanical properties of the fittings. It can improve their strength and ductility, ensuring that the fittings can withstand high-pressure environments.
4. Surface Finishing
The surface of the fittings is then treated to improve resistance to wear and corrosion. Techniques such as plating or anodizing may be employed to extend the life of the fittings.
5. Quality Control
Quality control is an essential aspect of the manufacturing process. Rigorous testing and inspection are conducted to ensure each fitting meets industry standards and specifications. This ensures that every component is safe, reliable, and ready for use in demanding applications.
Why Choose Fitsch as Your Hydraulic Tube Fittings Manufacturer?
Choosing the right hydraulic tube fittings manufacturer is crucial for the success of your operations. Here’s why Fitsch stands out in the market:
1. Wide Range of Products
At Fitsch, we offer a comprehensive selection of hydraulic tube fittings, including compression fittings, flared fittings, and push-to-connect fittings. Whether you require standard sizes or custom solutions, we have you covered.
2. Exceptional Quality Standards
Our commitment to quality is unwavering. We implement stringent quality control measures to ensure that every product meets international safety and performance standards.
3. Expertise and Innovation
With years of experience in manufacturing, our team of experts continuously innovate and improve our product offerings. We stay updated with the latest industry trends and technological advancements to provide our customers with cutting-edge solutions.
4. Competitive Pricing
We understand the importance of cost-effective solutions in today’s market. Fitsch offers competitive pricing without compromising on quality, making us a preferred choice for many businesses.
5. Reliable Customer Support
Our customer support team is always ready to assist you, whether you need advice on product selection or assistance with orders. We pride ourselves on building strong relationships with our clients, ensuring their needs are met promptly.
Applications of Hydraulic Tube Fittings
Hydraulic tube fittings are utilized across various industries, and their applications are as diverse as the fittings themselves. Here are some notable applications:
1. Agricultural Equipment
In the agricultural sector, hydraulic fittings are used in tractors, harvesters, and various implements. They facilitate efficient operation and control of hydraulic systems used for lifting, plowing, and harvesting crops.
2. Industrial Machinery
Hydraulic machinery, like presses, forklifts, and robotic arms, heavily relies on hydraulic tube fittings. These components help manage fluid transfer to ensure smooth and powerful operations in manufacturing setups.
3. Oil and Gas Sector
The oil and gas industry utilizes hydraulic tube fittings in drilling equipment and extraction systems. Their ability to withstand high pressures and harsh environments makes them indispensable in this sector.
4. Marine Applications
Hydraulic systems on ships and offshore platforms require reliable fittings to ensure safety and functionality. Fittings manufactured by Fitsch are designed to meet the rigorous demands of marine environments.
Maintenance of Hydraulic Tube Fittings
To maximize the lifespan and performance of hydraulic tube fittings, regular maintenance is essential. Here are some maintenance tips:
- Inspect Regularly: Conduct routine checks for signs of wear, leaks, or corrosion.
- Ensure Proper Installation: Follow manufacturer guidelines during installation to achieve a secure fit.
- Use Compatible Fluids: Ensure that hydraulic fluids used are compatible with the fittings to prevent degradation.
- Perform Scheduled Replacements: Replace fittings according to the schedule recommended by the manufacturer.
Conclusion
In conclusion, investing in high-quality hydraulic tube fittings is paramount for ensuring the reliability and efficiency of hydraulic systems. As a Hydraulic Tube Fittings Manufacturer, Fitsch (available at fitsch.cn) is committed to providing businesses with top-tier fittings designed for a wide range of applications. With a focus on quality, innovation, and customer satisfaction, we are your ideal partner in achieving operational excellence. Explore our wide range of products today and experience the difference of working with a leader in the hydraulic fittings industry.
Hydraulic Tube Fittings Manufacturer